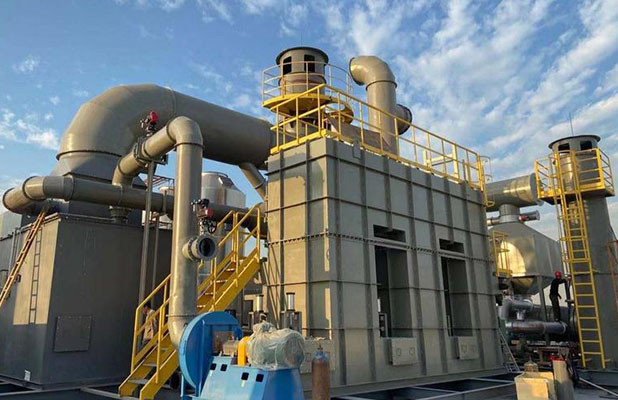
Regenerative Thermal Oxidation (RTO) is an efficient and energy-saving organic waste gas treatment technology widely used in various industries such as chemical, pharmaceutical, printing, painting, and petroleum refining. This technology decomposes harmful organic compounds (VOCs) through high-temperature oxidation, converting them into harmless carbon dioxide and water, while utilizing thermal storage materials to efficiently recover heat and significantly reduce energy consumption.
Working principle of RTO:
The core of the RTO system lies in its unique thermal storage heat exchange design. A system typically consists of three or more thermal storage chambers, each filled with high-efficiency ceramics or other high-performance thermal storage materials. The process flow is roughly as follows:
1. Preheating stage: The exhaust gas containing VOCs first passes through a heat storage chamber A that has been heated by high-temperature gas purified in the previous cycle. During this process, the exhaust gas is preheated to near the combustion temperature, while the heat storage material gradually cools down.
2. Oxidative combustion: The preheated exhaust gas then enters the combustion chamber. At high temperatures (usually above 760 ° C), VOCs undergo oxidation reactions with oxygen in the air, generating carbon dioxide and water vapor. This process does not require additional fuel or only requires a small amount of auxiliary fuel, especially when the VOC concentration is high enough, the system can even output heat from RTO.
3. Heat recovery and switching: The clean gas after combustion passes through another heat storage chamber (such as B), during which the high-temperature gas transfers heat to the heat storage material, and then the gas is discharged into the atmosphere. At the same time, the system automatically switches to the next cycle, and the originally cooled heat storage chamber A begins to receive new exhaust gas for preheating, while the original heat storage chamber B is ready to receive the next round of high-temperature purified gas for cooling, and this cycle repeats itself.
Technical advantages:
1. High thermal efficiency: The RTO system has a heat recovery rate of over 95%, significantly reducing operating costs, and is particularly suitable for continuous and high emission low concentration VOCs treatment.
2. Environmental compliance: Through high-temperature oxidation, the removal efficiency of VOCs can reach over 99%, meeting strict environmental emission standards.
3. Wide applicability: It can handle various VOCs containing exhaust gases, including corrosive or particulate gases, and is suitable for various industrial environments.
4. Easy maintenance: Using high-temperature and corrosion-resistant ceramic materials as heat storage media, the system is stable and reliable, and the maintenance cost is relatively low.
The Regenerative Thermal Oxidation (RTO) process has become one of the preferred technologies for treating organic waste gases due to its high efficiency, energy conservation, and environmental friendliness. With the progress of materials science and the continuous optimization of system design, the application scope and efficiency of RTO technology will be further expanded, contributing to the promotion of green industrial development.